Having replacement parts on-hand can help ensure continuity of laundry service during this crisis
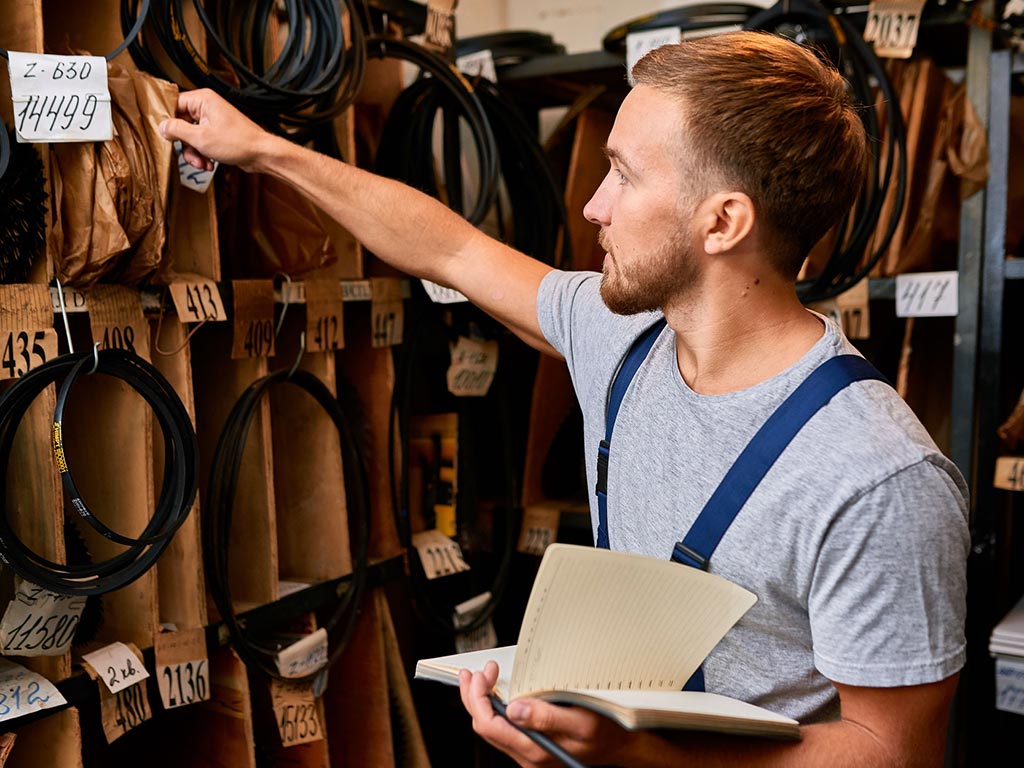
On-premises laundries have little tolerance for repairs and downtime during a normal period. Now, if you are serving a healthcare, long-term care, nursing home or fire/EMS facility during a pandemic, extended downtime is not an option. Situations are made even more difficult by safer–at–home lockdowns of these locations, limiting access to service technicians.
Being able to make minor repairs in-house can save valuable time. It’s worth noting that many UniMac distributors have curbside pickup options for parts stocked in-house and some will even drop ship to a facility at no cost. Alliance Laundry Systems and its facilities are considered essential and are shipping parts every day – hitting fast turnaround times and even offering next-day shipping on many items.
So, what parts should on-premises laundries have on-hand and be able to swap out? Drain valves would be at the top of that list. These are parts that open and close frequently; having extras is a good idea. Staff should also be able to diagnose a drain valve issue and swap the part out. Often, the “fix” is merely identifying the obstruction and removing it, which saves a service call…and valuable time.
Having fill valves on-hand and being able to make the 20- to 30-minute repair in-house, again saves a service call and any possible extended downtime. You’ll also want to have extra hoses and screens. Here again, educate staff on how to identify possible warning signs of an issue – slower-than-normal fill times. Have staff inspect fill hoses and screens on a regular basis.
Inverter filters are another simple part to have on-hand. Your laundry also should clean this simple part regularly to ensure the operation doesn’t incur a costly replacement of the washer-extractor’s inverter.
On the dry side, keep a couple replacement belts in–stock and lint screens. Perhaps more importantly, make sure staff is cleaning lint screens and keeping vents and burners clear of lint. Failing to keep your laundry equipment and ducts free of lint can be costly in terms of repairs and wasted resources.
While some repairs and maintenance can be managed in-house, it’s important for staff to know their limitations and when it makes sense to call an experienced service technician. Many UniMac distributors are offering reduced trip charges and some are even leveraging video troubleshooting to reduce time spent on-site.
Keeping on top of preventative maintenance as well as having a small a variety of replacement parts in-stock can help on-premises laundries avoid extended periods of downtime – something we can all agree that’s hugely important right now.